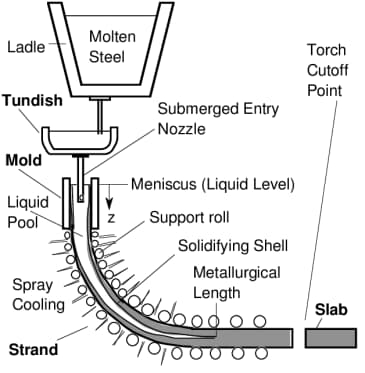
امروزه با پیشرفت در علم و فناوری و همچنین برداشتن قدمهای بزرگی در صنعت، مفهوم ریختهگری و انواع ریختهگری برای پاسخ به تقاضای کاربران به تولید محصولات پیچیده بیشتر از پیش به چشم میخورد. ریختهگری فرآیندی است که در طی آن محصولات پیچیده و دقیقی که نیازهای کاربر را رفع میکند، تولید میشود. ریختهگری انواع بسیاری دارد که در ادامه به معرفی آنها میپردازیم. اگر شما هم اهل صنعت و علاقهمند به موضوعات این حوزه هستید تا انتهای مقاله همراه ما باشید.
ریختهگری شامل مراحل اول تولید هر وسیلهای است. مراحلی که شامل ذوب کردن فلز و ریختن در قالب مخصوص و رساندن آن به دمای محیط برای شکلگیری وسیلهای که قصد تولید آن را داشتهایم، میشود. قطعا شما در فیلمهای تاریخی روند تولید شمشیر و وسایل آهنی را در آهنگری دیدهاید؛ این مثالی ساده برای قدمت و لمس بهتر این هنر است.
ریختهگری مانند هر حوزه صنعتی دیگری به چند شکل انجام میشود. تنوع وسایلی که توسط فرآیند ریختهگری تولید شده است، گستردگی در انواع ریختهگری را نشان میدهد.
ریختهگری شن و ماسه در فرآیند ریختهگری هر آلیاژ فلزی، آهنی و غیرآهنی به کار گرفته میشود. این ریختهگری در واقع همه کاره است. کاربرد ریختهگری شن و ماسه غالبا برای تولید انبوه در واحدهای صنعتی مانند قطعات ریختهگری فلزات خودرو است. قطعاتی مانند سرسیلندر، میللنگ وبلوک موتور توسط این فرآیند تولید میشوند.
قالبی که برای فرآیند ریختهگری شن و ماسه استفاده میشود از سیلیس است و شن و ماسه با پیوند طبیعی، قسمت سطح صاف قالب را میپوشانند. قالب دارای 2 سطح است؛ قسمت نیمه بالایی آن کوپ و قسمت نیمه پایینی آن کشیدن نامیده میشود. هنگامی که فلز مذاب شده باشد با پیمانه مخصوص که اصطلاحا آن را فنجان ریختن نیز مینامند، در داخل الگو یا همان قالب میریزند و صبر میکنند تا جامد شود و شکل نهایی خود را نشان دهد. در پایان کار با برش فلز اضافی فرآیند تکمیل شدن محصول نهایی ریختهگری فلزی تمام میشود.
ریختهگری قالب دائمی نام دیگر ریختهگری گرانشی است که با این نام در بین انواع ریختهگری شناخته شده است. در ریختهگری گرانشی ریختن مستقیم فلز مذاب در داخل حفره توسط تاثیر جاذبه انجام میشود. برای کنترل فرآیند ریختهگری میتوان قالب را کج کرد تا پر شدن بهتر صورت گیرد. بعد از پر کردن قالب به فلز فرصت داده میشود تا سرد شود و جامد گردد تا محصول تشکیل شود. فرآیند ریختهگری گرانشی برای فلزاتی مانند آلیاژهای سرب، روی، منیزیم، برنزهای خاص، چدن و آلومینیوم کاربرد دارد.
ریختهگری قالبی از قالبهای قابل استفاده دوباره ساخته شده از ترکیباتی مانند گرافیت، فولاد و غیره برای ساخت فلز و آلیاژهای فلزی بهره میگیرد. قطعاتی که با این روش تولید میشوند شامل اتصالات لوله، پیستون موتور، چرخدنده، محفظه دنده و چرخ هستند. ریختهگری گرانشی نسبت به ریختهگری شن و ماسه پرکاربردتر است؛ ولی از آنجایی که قالبهای فلزی گران قیمت هستند، باعث افزایش هزینه میشود.
ریختهگری تحت فشار دو نوع است که بستگی به سطح فشار دارد. ریختهگری فشار بالا برای تولید انبوه هندسهای پیچیده که نیاز به ظرافت و دقت بالایی دارند، بیشتر کاربرد دارد. این درحالی است که از ریختهگری تحت فشار پایین برای تولید قطعات بزرگ و ساده میشود. فلزات و آلیاژهای غیر آهنی مانند روی، قلع، مس و آلومینیوم در قالب قابل استفاده مجدد که توسط روانکننده سطح آن پوشانده شده است، با فشار بالا تزریق میشوند.
در طی فرآیند تزریق سریع، فشار بالا برای جلوگیری از سخت شدن فلز باید حفظ شود و بعد از پایان کار به حذف بخشهای اضافی پرداخته میشود. نحوه پر کردن قالب در ریختهگری گرانشی با ریختهگری تحت فشار متفاوت است. در اینجا قالب کج نمیشود و مرحله تزریق سریع صورت میگیرد تا فلز سریعتر جامد شود.
ریختهگری سرمایه گذاری، ریختهگری موم گمشده نیز نامیده میشود. در این نوع از انواع ریختهگری الگوی موم را توسط مواد نسوز و یک ماده اتصالدهنده برای شکل دادن به قالب سرامیکی یکبار مصرف تزریق میکند. بعد از آن فلزی که در اثر حرارت مذاب شده است، برای ساخت قالبهای فلزی در قالب ریخته میشود.
ریختهگری سرمایهگذاری یکی از انواع ریختهگری هایی است که به صرف هزینه و زمان و زحمت بسیار نیاز دارد . برای تولیدات انبوه و ریختهگریهای پیچیده که منجر به تولید چرخدنده، تنه دوچرخه، دیسکهای موتور و قطعات یدکی در ماشینهای انفجار، از ریختهگری سرمایهگذاری بهره میبرند.
قالبی که در ریختهگری گچ مورد استفاده قرار میگیرد، از مخلوطی به نام گچ پاریس ساخته شده است. ریختهگری گچ شباهت بسیاری به ریختهگری شن و ماسه دارد؛ اما با یکدگیر متفاوت نیز هستند. یکی از تفاوتها، روند کند خنک و جامد شدن فلز به علت رسانایی حرارتی پایین و ظرفیت گرمایی گچ است.
روند کند جامد شدن مزیتی برای تولید قطعات با مقطع نازک است؛ درحالی که کند سرد شدن برای مواد آهنی با دمای بالا مناسب نخواهد بود. ریختهگریهای کوچکی که حدود 30 گرم و ریختهگریهای بزرگی حدود 45 کیلوگرم را به راحتی با استفاده از ریختهگری قالب گچ میتوان تولید کرد.
ریختهگری روتو نام دیگری برای ریختهگری گریز از مرکز است. ریختهگری گریز از مرکز برای تولید صنعتی استوانهای از طریق نیروهای گریز از مرکز مورد استفاده قرار میگیرد. فرآیند این ریختهگری به این شکل است که فلز مذاب در قالب ریسندگی که از پیش گرم شده است، ریخته میشود و توزیع فلز در قالب توسط نیروهای گریز از مرکز در فشار بالا صورت میگیرد.
این ریختهگری سه نوع دارد: ریختهگری گریز از مرکز واقعی، ریختهگری نیمه گریز از مرکز و ریختهگری گریز از مرکز عمودی. قطعاتی مانند یاتاقان بوش، صفحات کلاچ، رینگهای پیستون و آستر سیلندر از جمله محصولاتی هستند که توسط ریختهگری گریز از مرکز تولید میشوند.
ریختهگری فوم گم شده شباهت بسیاری به ریختهگری سرمایهگذاری دارد؛ اما در ریختهگری لاست فوم از فوم برای الگو استفاده میکنند. پس از تشکیل قالب یا همان الگو، پوشش توسط سرامیک نسوز با غوطهور کردن، پوشش دادن، اسپری کردن یا برس زدن تکمیل میشود و بعد از انجام این مراحل فلز مذاب در قالب ریخته میشود تا محصول تولید شود.
فولاد آلیاژی، فولاد کربنی، چدن آلیاژی و آلیاژ آهنی از جمله موادی هستند که از طریق ریختهگری فوم از دست رفته میتوان از آنها محصولاتی را تولید کرد. محصولاتی مانند محفظه پمپ، شیر آتشنشانی، شیرها و اتصالات از جمله محصولاتی هستند که از این ریختهگری به دست آمدهاند.
ریختهگری خلاء تحت فشار خلاء 100 بار یا کمتر انجام میشود و علت آن خروج گاز از حفره قالب است. فلز مذاب برای از بین بردن حبابها و حفرههای هوا، داخل حفره قالب در محفظه خلاء ریخته میشود. از بین بردن خلاء حفره قالب مانع از گیر افتادن گازها در داخل حفره در طی فرآیند تزریق فلز خواهد شد و به این شکل فلز در این محفظه حرارتی پخته میشود و از قالب، آن را خارج میکنند.
ریختهگری در خلاء از فرآیندهایی است که در صنایع مختلفی مانند خودرو، هوافضا، الکترونیک، دریایی، مخابرات به کار گرفته میشود. اجزای ساختاری شاسی و قطعات بدنه خودرو از جمله محصولاتی است که در اطراف شما بسیار به چشم میخورد و توسط همین فرآیند ساخته شده است.
ریختهگری فشرده که به آن آهنگری مایع نیز گفته میشود، نوعی از انواع ریختهگری است که طی آن فلز ترکیبی به دست میآید و ریختهگری قالب دائمی و آهنگری قالب در یک مرحله با هم ادغام میشود. مقدار تعیین شدهای از آلیاژ فلز مذاب داخل قالب تزریق شده است و تحت فشار قرار میگیرد و بعد از آن بخش فلزی در دمای ذوب حرارت داده شده و از قالب خارج میشود.
این ریختهگری برای تولیدات انبوه بسیار مناسب نیست و از طریق فشار زیادی که در طول انجماد وارد میشود به جلوگیری از انقباض و تخلخل کمک بسیاری میکند. این ریختهگری یک فرآیند بالقوه برای قطعات حیاتی ایمنی در سیستمهای خودرو مثل اتصالات اسپیس فریم، بندهای آلومینیومی فرمان جلو، فریم شاسی، براکتها گرهها است.
ریختهگری مداوم به این شکل است که فلز پس ذوب شدن در قالبی با آب خنک و انتهای باز ریخته میشود و سطح آن شروع به جامد شدن بر سطح مایع میکند؛ در واقع فرآیند سرد شدن از بیرون به سمت داخل اتفاق میافتد. بعد از پایان این مرحله رشتههای فلزی را میتوان از قالب خارج کرد و طولهای اضافی از پیش تعیین شده را به وسیله قیچی مکانیکی یا مشعلهای اکسیاستیلن متحرک جدا کرد.
تولید انبوه پروفیلهای فلزی با سطح مقطع ثابت با ریختهگری مداوم به راحتی امکانپذیر است. تولید میلههای فولادی غالبا با این روش رایج است و ریختهگری عمودی و نیمه پیوسته مانند بیلت، شمش و میله نیز از همین طریق صورت میگیرد. محصولاتی که از این روش به دست میآیند همگن، یکدست و متراکم هستند.
قالبگیری پیوسته شبیه به ریختهگری شن و ماسه است؛ فقط در این روش پوسته سخت شده ماسه حفره قالب را تشکیل میدهد؛ درواقع فرآیند ریختهگری قالب قابل مصرف است. ماسه این که در طی این فرآیند مورد استفاده قرار میگیرد، ریزتر از ماسهای است که در ریختهگری شن و ماسه استفاده میشود. در این نوع از انواع ریختهگری ماسه با رزین ترکیب شده تا به راحتی حرارت ببیند و در پوسته اطراف الگوی سخت کرد.
قالبگیری پوسته محدودیت اندازه و وزن قطعات را دارد و محصولات تولید شده سطح و دقت ابعادی خوبی دارند. محصولات صنعتی مانند محفظه گیربکس، شاتون، قایقهای کوچک، هود کامیون، میل بادامک و غیره از جمله مواردی هستند که از این طریق تولید میشوند.
کلام آخر
ریختهگری حوزه بسیار بزرگی از صنعت را شامل میشود که انواع آن منجر به تولید محصولاتی است که روزانه از آنها استفاده میکنیم و تاثیر به سزایی در کیفیت زندگی ما گذاشته است. اکثر وسایلی که در اطراف شما هستند، توسط یکی از انواع ریختهگری تولید می شوند و شما را در داشتن زندگی راحت یاری میکند.
منبع: https://www.rapiddirect.com/blog/different-types-of-casting-process/